Graphene |
Hypersonics |
U-TBCC |
U-GTG |
Motors & Rotors |
Conforming Tanks |
Primary ION Drives (Space)
IO Aircraft Technologies
Hypersonics

NOTE: ALL engineering and physics
of our hypersonic developments and scramjet engineering, is minimum 30 years
more advanced then all programs in existence. Because of this, we are extremely
protective of engineering details.
Short list for innovations and advances in hypersonic technologies.
Every aspect of our hypersonics engineering and physics is multiple decades
ahead of all programs in existence. While others work within a box, we don't
have a box, we burned it.
Utilizing new methods of fabrication and construction, makes it possible
to use advanced additive manufacturing, dramatically reducing the time and costs
associated with producing hypersonic platforms from missiles, aircraft, and space
capable craft. Instead of aircraft being produced in pieces, then bolted
together; small platforms can be produced as a single units and large
platforms can be produced in large sections and then mated together without bolting.
These techniques include using exotic materials and advanced assembly
processes that are currently unheard and not research programs exist
outside of our own techniques, with an end result of streamlining the production
time and
costs for hypersonic aircraft; reducing months of assembly to weeks, and
weeks to days.
Overall, this process greatly reduces the cost for producing hypersonic
platforms and any other very high end application usage. Even to such an extent that
currently a Hellfire missile costs apx
$100,000 but by utilizing our technologies, replacing it with a Mach
8-10 hypersonic missile (See our Zircoff platform) of our physics/engineering and that missile
would cost roughly $75,000 each delivered delivered.
Materials used for these manufacturing processes are not disclosed, but
overall, provides a foundation for extremely high stresses and
thermodynamics far beyond all current development programs, ideal for hypersonic platforms
and space capable platforms requiring re-entry into atmosphere. This
specific methodology and materials applications is many decades ahead of
all known programs.
*Note, most entities that are experimenting with additive
manufacturing for hypersonic aircraft, this makes it mainstream and
standardized processes, which also applies for mass production.
What would normally be measured in years of development and perhaps a decade to go from
drawing board to test flights, is reduced to singular months and ready
for production within a year maximum.
Dramatically Increasing the efficiency of
fuel air mixture for combustion processes at hypersonic velocities within
scramjet propulsion platforms.
The
technical aspects of these processes are non disclosable.
For optimal scramjet ignition, a process
known as Self Start is sought after, but in many cases if the platform
becomes out of attitude or less then ideal conditions, the scramjet will not ignite and viscosity will
become far too turbulent for fuel/air mixture to become combustible at
hypersonic velocities resulting in not being capable of producing
positive thrust. We have already
solved this problem which as a result, a scramjet propulsion system can
ignite at lower velocities and higher velocities, at optimal attitude or not
optimal attitude. It doesn't matter, it will ignite anyways at the
proper point for maximum thrust capabilities at hypersonic velocities.
More importantly, this process is able to operate from lower altitude
below 15,000ft ASL through 100,000+ ft ASL, without needing to
re-engineer the isolator, combustion, or nozzle sections of the scramjet
platform. Resulting in a single baseline process that is
optimized for all conditions.
The
technical aspects of these processes are non disclosable.
Kerosene is an easy fuel to work with, and
most western nations developing scramjet platforms use Kerosene for that
reason. However, while kerosene has better thermal properties then
Hydrogen for lower velocities, Hydrogen is a far superior fuel source in scramjet propulsion
flight at higher velocities and MUCH less fuel weight, due it having a much higher efficiency capability
ie impulse subject matters. Because of
this aspect, in conjunction with our developments and capable of
managing much higher thermal properties then such entities as Lockheed,
Boeing, Aerojet, and Raytheon, it allows for a greatly improved fuel to air mixture, combustion, thrust; and ability for
much higher thrust at increased hypersonic velocities instead of very low hypersonic velocities in the Mach 5-6
range. Instead, Mach 8-10 range is the norm for our hypersonic physics
and engineering, while we have begun developing
hypersonic capabilities to exceed Mach 15 in atmosphere within less then 5
years.
While other entities keep rehashing the same engineering
principles from the 1990's and keep repeating the same academics
research over and over for 20 years, trying to discover small incremental
advances of old technology, we are developing new methodologies and
focus on hydrogen fuel, eliminating kerosene entirely.
In conjunction with both our
advances in technologies plus conforming high pressure storage, we are
easily able to lower the launch weight of a scramjet missile by an
average of 40% and an increase in fuel capacity by 200-300%, thus much
longer range and much higher velocities. In comparison to
such platforms like the X-51, which weighs 1,226 LBS without booster, if
we had built a similar missile, the weight would had been roughly 750
LBS with 300% higher fuel capacity surpassing 600 seconds under power.
For laymen's, in common terms, Kerosene is 25 Octane, while Hydrogen
is 130 Octane. Similar to drag cars. Gasoline powered cars
can produce a lot of horsepower, but top fuelers run on Alcohol.
It's night and day. Same principles apply for ramjets and
scramjets, Hydrogen is a much hotter fuel then kerosene. We're
developing the top fuelers for hypersonics, while everyone else are
stuck on gasoline.
As most know in hypersonics, Hydrogen is a
superior fuel source, but due to the storage abilities, can only be
stored in cylinders thus much less fuel supply. Not anymore, we
have developed conforming high pressure tank technology for use in
aerospace, automotive sectors, maritime, etc; which means any overall
shape required for 8,000+ PSI CNG or Hydrogen. For
hypersonic platforms, this means the ability to store a much larger
volume of hydrogen vs cylinders. These tanks are not fragile either.
Easily able to surpass 500,000 PSI tensile strength, the tanks are
incorporated into the airframes themselves and become the backbone of
the internal airframe, because it is able to manage the very intense
pressures involved, that also means a dramatic decrease in airframe
weight.
As an example, X-43 flown by Nasa which flew
at Mach 9.97. The fuel source was Hydrogen, which is extremely more
volatile and combustible then kerosene (JP-7), via a cylinder in the
main body. If it had used our technology, that entire section of the
airframe would had been an 8,000 PSI H2 tank, which would had yielded
5-6 times the capacity. While the X-43 flew 11 seconds under power
at Mach 9.97, at 6 times the fuel capacity would had yielded apx
66 seconds of fuel under power at Mach 9.97. If it had flew
slower, around Mach 6, same principles applied would had yielded apx 500 seconds of fuel supply under power (slower speeds required less
energy to maintain).
Due to these subject matters, weight equals drag in
aerospace. Same goes for hypersonics, the more the weight, the more
thrust is required for acceleration and maintaining velocity. We shed a
massive amount of weight overall, up to 50% total flight weight
reduction. Which results in MUCH higher thrust to weight ratio, but also
requires much less fuel to maintain Mach 8-10 velocities, extending the
range of the aircraft greatly.
The
technical aspects of this engineering is non disclosable.
Normally, fuel injection is conducted at the
correct insertion point within the shock train for maximum
burn/combustion. Our methodologies differ, since almost half the fuel
injection is conducted PRE shock train within the isolator, so at the
point of isolator injection the fuel enhances the combustion process,
which then requires less fuel injection to reach the same level of
thrust capabilities.
Smoother interaction at hypersonic
velocities and mitigating heat/stresses for beyond Mach 6
thermodynamics, which extraordinarily improves Type 3, 4, and 5 shock
interaction.
Additionally, mitigation and
active management of boundary layer separation, including extensive
reduction in separation bubble interaction within isolators and
combustion regions of scramjet systems. This leads to greatly enhanced
fuel/air mixture and improving optimal ignition, and active shock train
management in flight.
Image: Root of AFRL funding for boundary layer separation, derives
from developments by IO Aircraft
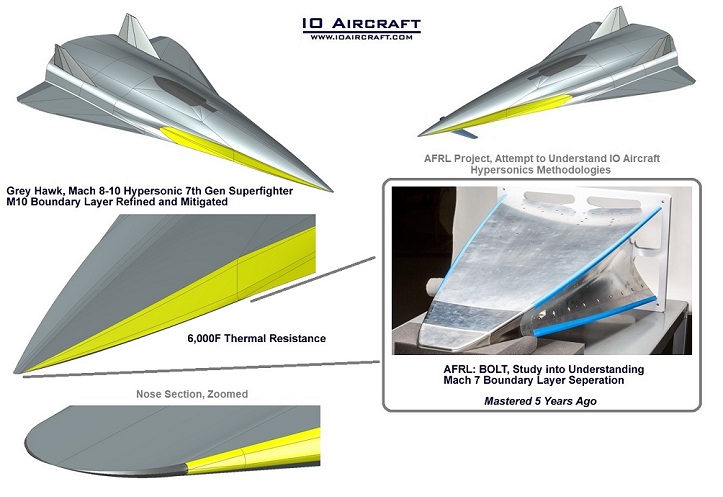
To date, the maximum thermal resistance was
tested at AFRL in the spring of 2018, which resulted in a 3,200F thermal
resistance for a short duration. This technology, allows for normalized
hypersonic thermal resistance of 3,000-3,500F sustained, and up to 6,500F
resistance for short endurance, ie 90 seconds or less. 10-20 minute
resistance estimate approximately 4,500F +/- 200F.
*** This technology advancement also
applies to Aerospike rocket engines, in which it is common for
Aerospike's to exceed 4,500-5,000F temperatures, which results in the
melting of the reversed bell housing. That melting no longer
occurs, providing for stable combustion to occur for the entire flight
envelope
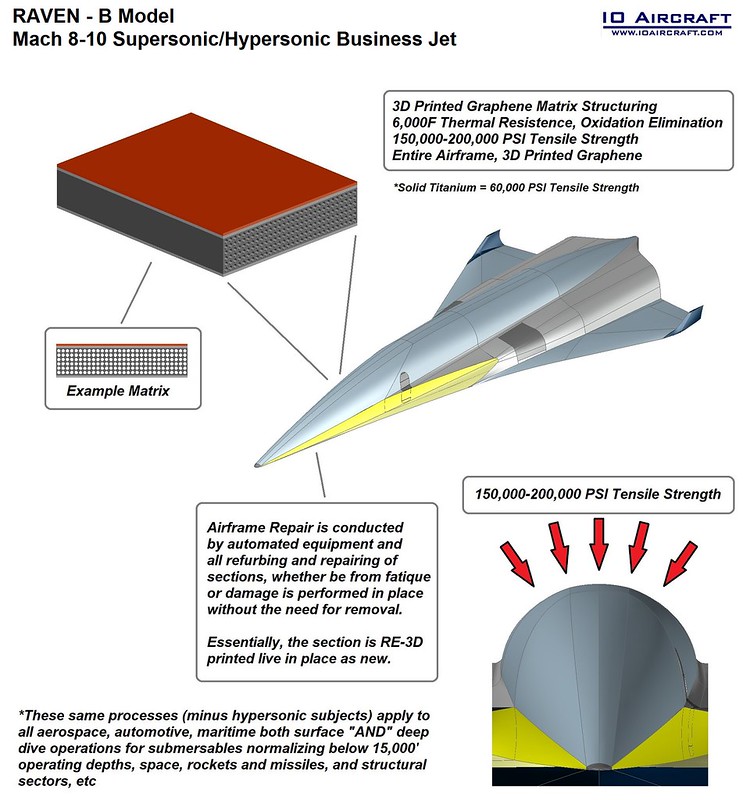
With old technologies, side wall cooling
within the isolator and combustion region is
required for hypersonic flight and scramjet propulsion systems,
otherwise the isolator and combustion regions of a scramjet would melt,
even using advanced ablatives and ceramics, due to
their inability to cope with very high temperatures. Using technology we
have developed for very high thermodynamics and high stresses (50,000+
psi), side wall
cooling is no longer required, thus removing that variable from the
design process entirely and focusing on improved ignition processes and
increasing net thrust variables.
Active and adaptive flight dynamics,
resulting in the ability for scramjet ignition at a much lower velocity,
ie within ramjet envelope, between Mach 2-4, and seamless
transition from supersonic to hypersonic velocities, ie supersonic ramjet
(scramjet). This active and dynamic aspect, has a wide variety of
parameters for many flight dynamics, velocities, and altitudes; which
means platforms no longer need to be engineered for specific altitude
ranges or preset velocities, but those parameters can then be selected
during launch configuration and are able to adapt actively in flight.
Thus result for optimal flight performance across the entire spectrum of
velocity and altitude desired.
Hypersonic vehicles, like their
less technologically advanced brethren, use large actuators and the
developers hope those controls surfaces do not disintegrate in flight.
In reality, it is like rolling the dice, they may or may not survive,
hence another reason why the attempt to keep velocities to Mach 6 or
below. We have shrunken down control actuators while almost doubling
torque and response capabilities specifically for hypersonic
dynamics and extreme stresses involved, which make it possible for
maximum input authority for Mach 10 and beyond. Our engineering on
this subject matter is developed for Mach 15+ threshold in atmosphere.
To date, most control surfaces
for hypersonic missile platforms still use fins, similar to lower speed
conventional missiles, and some using ducted fins, same as the previous
listed subject. This is mostly due to
lack of comprehension of hypersonic velocities and using those physics in the
platforms own favor.
Instead, the body itself incorporates those control surfaces, greatly
enhancing the airframe strength, opening up more space for hardware and
fuel capacity; while simultaneously enhancing the platforms maneuvering
capabilities. So instead of the aircraft needed to fly straight
and level, it is able to actually maneuver at extreme velocities
and not disintegrate in flight.
This results in scramjets missile
that can fly like conventional missile
platforms, and not straight and level at high altitudes, losing velocity
on it's decent trajectory to target. Another added benefit to this
aspect, is the ability to extend range greatly, so if anyone else's
hypersonic missile platform were developed for 400 mile range, falling
out of the sky due to lack of glide capabilities and has to dive to
target rapidly to maintain control; our platforms can
easily reach 600+ miles, with minimal glide
deceleration and as it approaches its target can then nose over and dive
in on it. *Another aspect of that is re-ignition of the
scramjet on approach to target and accelerating to impact for dramatic
increase in kinetic energy delivery.
|
|
|
Space Plane, Single Stage to Orbit, Hypersonic Plane, Hypersonic Aircraft, Hypersonic Jet, scramjet, ramjet, turbine based combined cycle, glide breaker, hypersonic, hypersonic weapon, hypersonic missile, Air Launched Rapid Response Weapon, ARRW, scramjet missile, boost glide, tactical glide vehicle, phantom works, skunk works, htv, hypersonic tactical vehicle, afrl, onr, boeing, utc, utx, ge, TBCC, RBCC, Reaction Engines, plane, turbine, spacex, virgin orbit, virgin galactic, usaf, single stage to orbit, sto, space plane, falcon heavy, delta iv, hypersonic commercial aircraft, hypersonic commercial plane, hypersonic aircraft, hypersonic plane, ICAO, boeing phantom express, phantom works, boeing phantom works, lockheed skunk works, hypersonic weapon, hypersonic missile, scramjet engineering, scramjet physics, scramjet, ramjet, dual mode ramjet, darpa, onr, navair, afrl, aerion supersonic, aerion, spike aerospace, boom supersonic, air taxi, vtol, personal air vehicle, vertical take off and landing, urban air mobility, ultralight, far 103, experimental, type certified, dual mode ramjet, scramjet engineering, scramjet physics, hypersonic weapons, hypersonic missiles, boost glide, tactical glide vehicle, phantom express, xs-1, htv, Air-Launched Rapid Response Weapon, ARRW, hypersonic tactical vehicle
|
|